(Please go to our Press Center for pdf versions)
Swedish Company Launches World’s Hardest Steel
Steel that does not need forging or machining to turn into a finished product. The hardest and most wear-resistant metal on the market. Any shape you wish can be produced. And as a bonus, considerably less material is consumed. Swedish company VBN Components continues to make steel history.
VBN Components, based in Uppsala, Sweden, produces steel using additive manufacturing, so-called 3D-printing. This means that metal powder is melted layer-by-layer into the shape of your choice. The company’s technology makes it possible to manufacture industrial tools and components, such as drills and cutters, in the shape end-users choose and in metals of extremely high quality. Its new steel has a wear resistance that substantially increases the life-span and efficiency of products, which also lowers material consumption. In contrast, traditional steel manufacturing is not able to produce a tool with the qualities of this new steel: it would be too hard to process, cut or shape, for example.
“The limitations of traditionally-made products result in a compromise. Instead of choosing the material best-suited to the product in mind, producers are instead forced to use a material that they can process. By focusing on material performance, we turn this completely around”, says Martin Nilsson, CEO of VBN Components.
Large market
VBN Components’ new, wear-resistant steel is unique. The engineering industry has a constant need to find tool and component materials with increased wear and heat resistance, but until now has come up against numerous obstacles to finding the ideal material. The properties of the new steel not only overcome these limitations, but also shorten lead-times thanks to fewer processing steps. Companies using these products will increase productivity, thereby saving money, and lower their environmental impact. What’s more, competitors are far behind in wear resistance. This makes VBN Components’ worldwide market very large.
VBN Components has been producing extremely hard and wear-resistant steel products using this technique for many years. Step-by-step, the company has moved towards what is today the world’s hardest steel – a milestone in materials development.
The need for less material in both end-use and manufacturing is one of the reasons why environmental impact is reduced by 90% compared to traditional industry (according to tests at one large Swedish company).
“Many people we’ve talked to have doubted that we could achieve ‘the impossible’. Today we’re very proud to introduce this unique metal. Its users will enjoy all its aspects of more environmentally-friendly manufacturing and be able to increase their competitiveness”, says Ulrik Beste, CTO of VBN Components.
For further information, please contact:
Isabelle Bodén, Press Contacts
VBN Components AB
Switchboard: +46 (0)18-24 07 60
Cell phone: +46(0)702-36 22 81
Email: Isabelle.boden@vbncomponents.com
Website: www.vbncomponents.com
Press Center: https://vbncomponents.com/press/
VBN Components in brief
VBN Components AB is a frontline materials development company that manufactures wear-resistant metal components directly from powder, so-called 3D-printing (additive manufacturing, free forming). The company, which has won numerous awards, is conducting a range of important customized projects to improve the competitiveness of the engineering industry. An alumnus from Uppsala Innovation Centre, ranked as the world’s 10th best business incubator, VBN is supported by the Swedish Energy Agency. The company provides Near-Net-Shape components branded Vibenite® to clients needing metal components with high complexity and/or extreme wear-resistance. www.vbncomponents.com
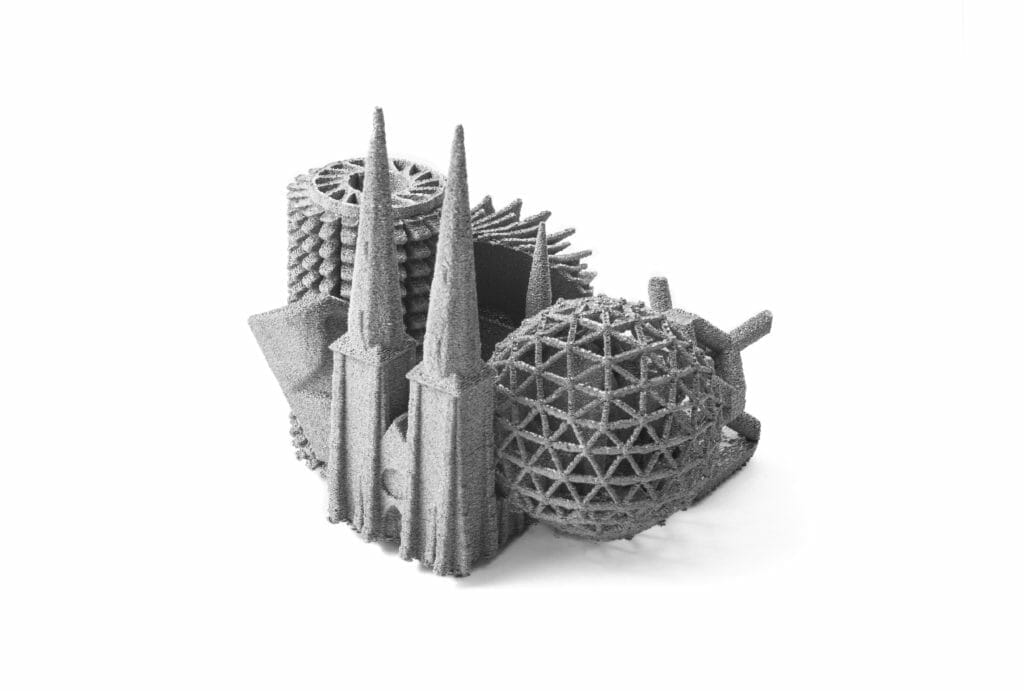
PRESSMEDDELANDE 27 November 2017
(Vänligen se vårt pressrum för pdf-versioner)
Svenskt företag lanserar världens hårdaste stål
Stål som varken kräver smide eller skärande bearbetning för att bli en färdig produkt. En metall som är den hårdaste och mest nötningståliga på marknaden. De former man önskar går att tillverka. Dessutom går det åt betydligt mindre material. Företaget VBN Components fortsätter skriva svensk stålhistoria.
VBN Components, baserat i Uppsala, tillverkar stål genom additiv tillverkning, så kallad 3d-printning. Det innebär att metallpulver smälts i lager på lager till önskad form. Företagets teknologi gör det möjligt att tillverka industriella verktyg och komponenter, till exempel borrar och fräsar, i de former man önskar och i metaller av extremt hög kvalitet. Företagets nya stål har en nötningstålighet som kraftigt ökar livslängden och effektiviteten på produkter, vilket också innebär minskat materialbehov. Genom traditionell ståltillverkning är det inte möjligt att tillverka ett verktyg med det nya stålets kvaliteter. Det vore för hårt att processa, för svårt att skära i eller att forma.
”Begränsningarna hos traditionellt tillverkade produkter resulterar i en kompromiss. Istället för att välja det material som bäst passar slutprodukten, måste man välja det material som kan tillverkas. Vi vänder på det och arbetar med fokus på materialprestanda”, säger Martin Nilsson, VD på VBN Components.
Stor marknad
Det nya stålet är unikt. Konkurrenter på marknaden ligger långt efter i nötningstålighet. Verkstadsindustrin har ständigt behov av att hitta material som har bättre nötnings- och värmetålighet för specifika syften. Tidigare har man ofta stött på otaliga begränsningar i sina ansträngningar att hitta det bästa materialet för verktyg och komponenter. Det nya stålet har en nötningstålighet som kraftigt ökar livslängden och effektiviteten på produkterna. Dessutom minskar ledtiden avsevärt tack vare färre processteg. De företag som använder produkterna kommer att öka sin produktivitet, dvs spara pengar, och minska miljöbelastningen.
VBN Components har tillverkat stålprodukter med denna teknik i flera år; extremt hårt och nötningståligt stål. Steg för steg har företaget tagit sig till det som idag är världens hårdaste stål, en milstolpe inom materialutveckling.
Behovet av mindre material vid slutanvändningen och vid själva tillverkningen är ett av skälen till att miljöpåverkan reduceras med ungefär 90 % jämfört med traditionell industri (visat hos svenskt verkstadsföretag).
”Många vi pratat med inom branschen har tvivlat på att vi skulle lyckas med ’det omöjliga’. Idag är vi väldigt stolta över att introducera denna unika metall med allt vad den
innebär för en miljövänligare tillverkningsprocess och för kunders konkurrenskraft”, säger Ulrik Beste, Teknisk chef på VBN Components.
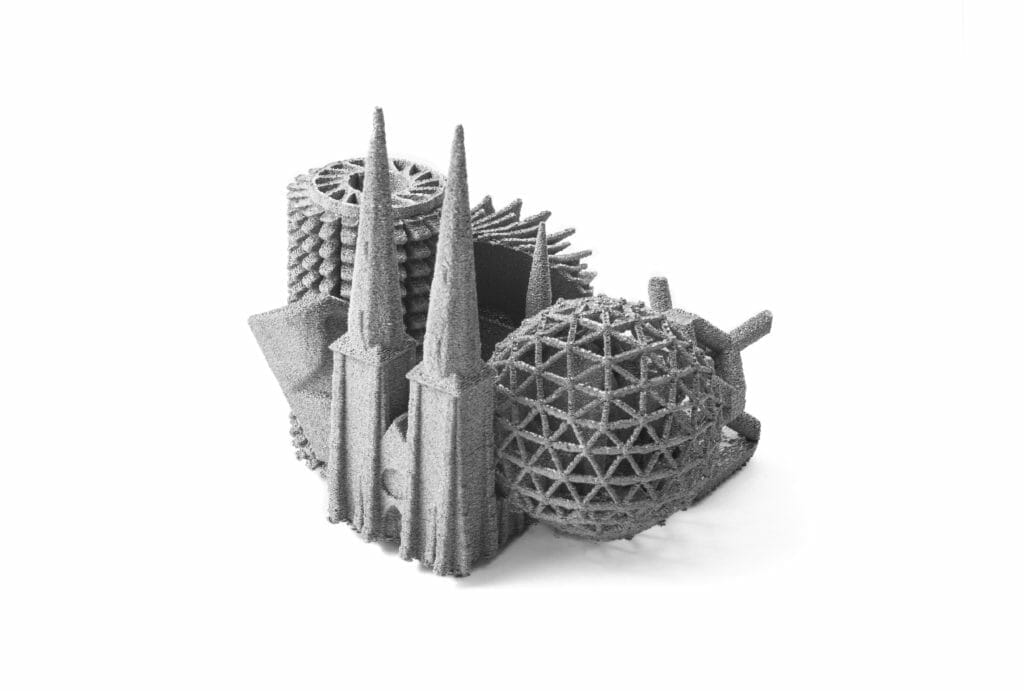
För vidare information, vänligen kontakta:
Isabelle Bodén, Presskontakter
VBN Components AB
Växel: +46 (0)18-24 07 60
Mobil: +46(0)702-36 22 81
Email: Isabelle.boden@vbncomponents.com
Presscenter: https://vbncomponents.com/press/
Om VBN Components
VBN Components är ett svenskägt företag, grundat 2009 av Peter Vikner, Ulrik Beste och Martin Nilsson. Grundarna belönades år 2013 med Sveriges största uppfinnarpris, SKAPA Utvecklingsstipendium. Företaget tillverkar nötningståliga metallkomponenter direkt från pulver med s.k. 3D-printing (Additiv tillverkning, friformning) och är involverat i en rad kundanpassade projekt för att öka verkstadsindustrins konkurrenskraft. VBN är alumn från Uppsala Innovation Centre, rankat som världens tionde bästa företagsinkubator, och stöds även av Energimyndigheten. Företaget tillverkar komponenter i nära-färdig-form under varumärket Vibenite® till kunder som har behov av komplexa former och/eller extremt nötningsmotstånd. www.vbncomponents.com