PRESS RELEASE 3 DECEMBER 2018
A hard metal (cemented carbide) produced in a shape of the customer’s choice, without sintering or cutting. Minimal material waste. A patented alloy that is heat resistant up to 750°C. After years of research, VBN Components is the first company to succeed with this innovation.
VBN Components, the company that gave us ”The World’s Hardest Steel” in 2017 is now launching yet another milestone within materials development. After years of research the patented hard metal Vibenite® 480 is now ready. The alloy is corrosion resistant and also extremely heat and wear resistant. The fact that it is produced by additive manufacturing / 3D-printing is absolutely ground-breaking. It enables complex shapes for industrial tools and components and reduces environmental impact to an absolute minimum.
“It is a particular kind of joy for me, as a material developer, to introduce such ground-breaking news within the area of hard metals. We turn the page in the book of Swedish material history”, says Ulrik Beste, PhD Materials Science and Tribology, CTO of VBN Components.
Increased productivity and reduced environmental impact
Vibenite® 480 is based on metal powder produced through large scale industrial gas atomisation. This minimises both cost and environmental impact. The new material combines the toughness of powder metallurgy high speed steels (PM-HSS) with the heat resistance of cemented carbides, which is why this new group of materials is named hybrid carbides. Within 3D-printing it has long been a wish to produce alloys with high carbide content. VBN Components now proves, more than ever, that they master this technique. Their Vibenite® 480 has a carbide content of ~65%, making it tougher than regular hard metals and therefore suitable for more complex details.
Drilling, milling and turning are no longer needed. Mixing of powder, drying and pressing becomes redundant. Vibenite® 480 is niched both towards applications where steel is normally used, but where production efficiency could increase when changing to hard metal, and also towards hard metal applications with complex geometry.
Practically this means that metal cutting tools which today are manufactured through machining of steel bars, could be replaced by the hybrid carbide and run with higher speed, thanks to higher heat resistance. As mentioned, complex shapes is one of the benefits when 3D-printing Vibenite® 480, but you can also produce much larger objects in one single piece, than with traditional hard metal technique. This increases the number of possible usage areas and makes it easy to make prototypes; you can print 1, 10 or 1000 items from one or several prints.
“We have learned an enormous amount on how to 3D-print alloys with high carbide content and we see that there’s so much more to do within this area. We have opened a new window of opportunity where a number of new materials can be invented”, says Martin Nilsson, CEO of VBN Components.
VBN Components’ technology enables significantly shorter lead times and increased performance, as well as environmental benefits through large material savings and fewer transports. The material is well adapted for products with extreme demands of wear and heat resistance, such as tools for thermoforming, diecasting, cutting and woodworking. Rock drilling is another evident application where VBN Components has already started a collaboration with Swedish company Epiroc.
VBN Components will invite ”early adopters”, those who wish to be the first to enjoy the benefits of this technology, to a web conference. If you have an interest to participate, or want to know more about the material, please email: info@vbncomponents.com
Click here to watch the video about the new material.
Facts on hard metal / cemented carbideHard metal was first patented in Germany in the 1920’s, but did not really start to be used until the 1950’s. Back then, it was mostly used as a wear resistant material for tools used in light bulb production. Today hard metals are one of the most important material groups within rock drilling, metal cutting tools and other high wear components like valves and pumps. A typical hard metal has 10% Co and 90% carbides.
Facts Vibenite® 480Material type: Patented hybrid carbide / hard metal.Carbide content: ~65%Hardness: ~67 HRCHeat resistance: 750°CCorrosion resistantProduced with gas atomised metal powder through 3D-printning.
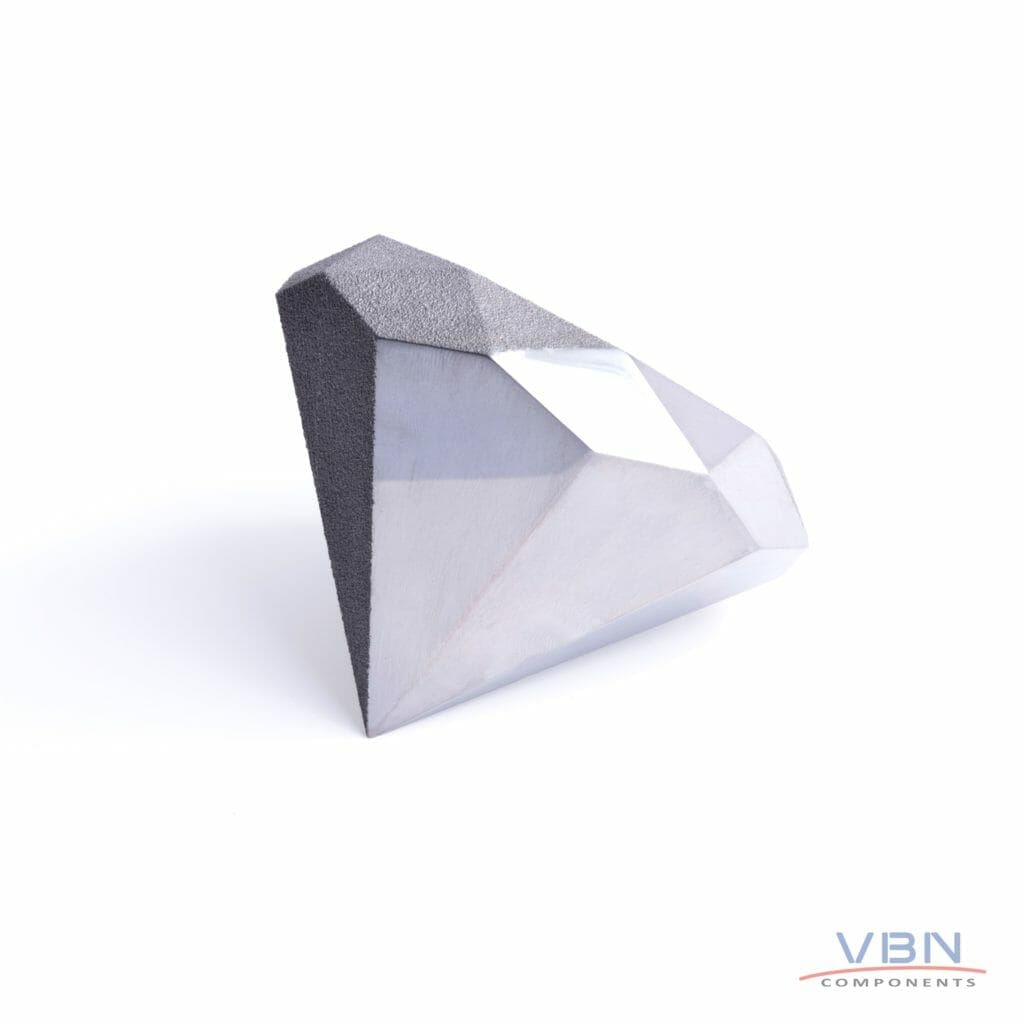
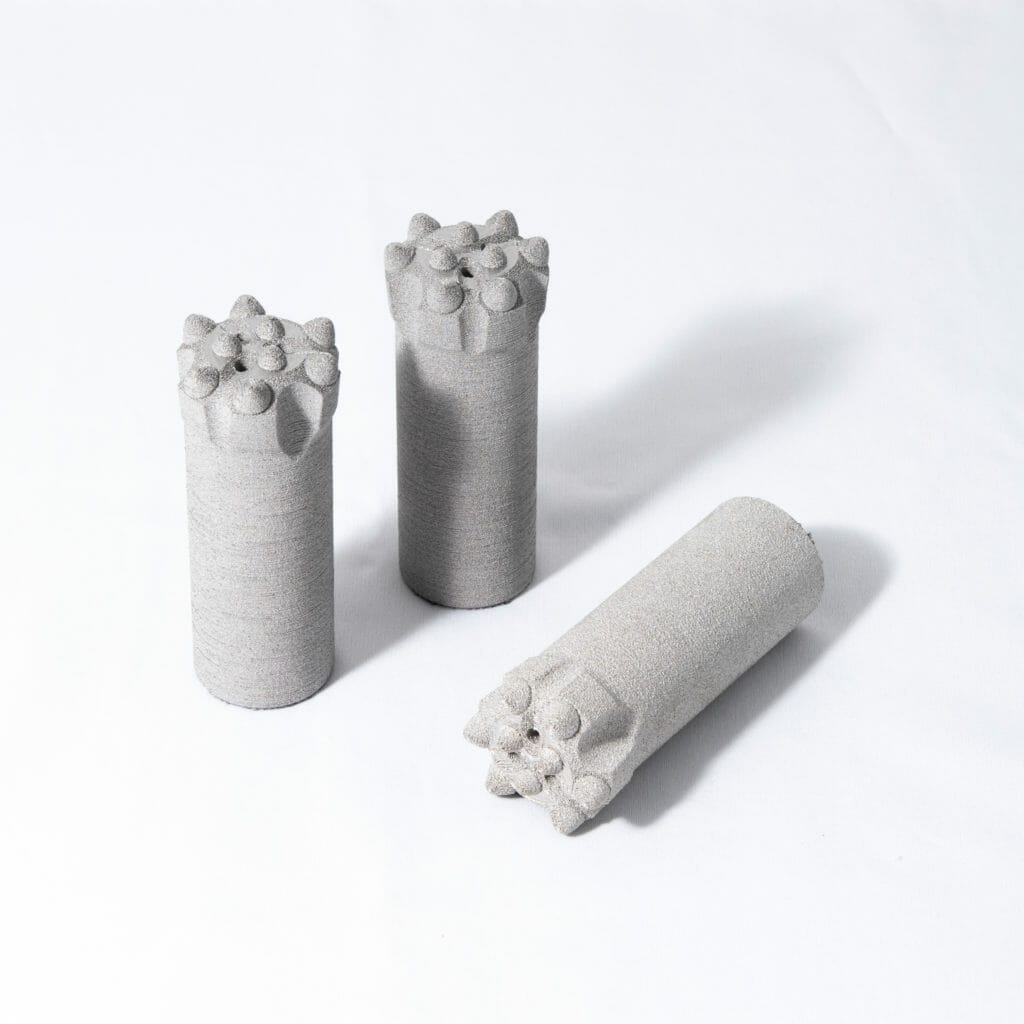