Dear friends,
It has been a year of many events. Those of you who follow us carefully have already read in previous newsletters about our collaboration with SKF, our partnership with Brazilian distributor Farcco Tecnologia, or the many tradeshows that we have attended. Now comes even more exciting news recaps about our new CEO, exceptional wear test results and a licence agreement with a large manufacturer of machining tools.
We are also very happy to announce that we will soon be in possession of a URQ-HIP machine, which will shorten our lead times and give us more control of the production chain. (More on this will follow, get in touch if you are interested in our HIP and heat treatment services for your own development or products.)

Magnus Bergman new CEO
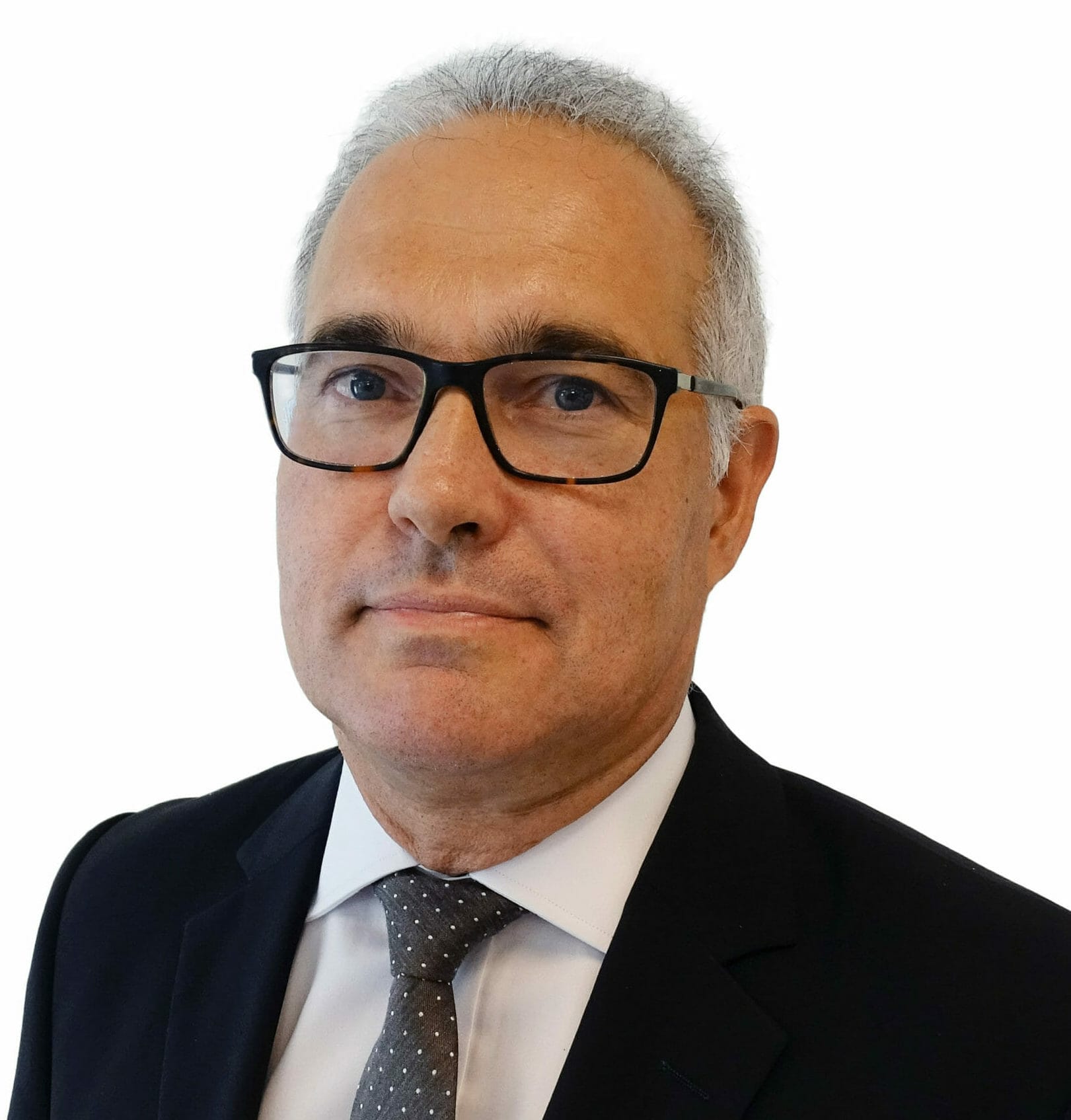
This autumn we welcomed our new CEO Magnus Bergman. Magnus Bergman has a master’s degree in Materials Science from KTH and has held several roles within the Sandvik Group with a focus on R&D, international sales, and management. He also has broad experience from the heat treatment industry and the machinery industry.
Licence agreement with ANAJ Czech

We are finishing off the year with great news about signing a licence agreement with one of the largest manufacturers of special machining tools in the Czech Republic. ANAJ Czech, a.s. has been successfully operating on the market for over 25 years and is a well-established player in Eastern Europe and in Germany. ANAJ will develop semi-finished tools for gear manufacturing (i.e. gear hobs and power skiving), using Vibenite® materials. In a later phase focus will also be on the development of tools for machining of non-ferrous alloys (Al, Ti and Mg). Check out the press release here.
Exceptional wear resistance for Vibenite® 350

A Vibenite® material that is usually not highlighted in the media is corrosion resistant Vibenite® 350. However, researchers at The University of Manchester have now measured its wear rate to be only 1/6 to 1/7 of the wear rate of conventionally processed austenitic stainless steel grades! This indicates an exceptional wear resistance, primarily attributed to microstructural features such as high carbon content, as well as size, shape and distribution of the carbides. The results are published in the open access article “Wear resistance of an additively manufactured high-carbon martensitic stainless steel” in Nature Scientific Reports.
Expansion in North America and Asia

In the past couple of years, VBN Components has increased sales in North America. As you might know, VBN delivered an important number of samples of three Vibenite® alloys to the US Armed Forces for testing in several applications and setups in 2021. That same year it was made official that the Vibenite® series of materials were being used by the Canadian engineering company Exergy Solutions, and that they would be printed with Calibur3 machines from UK based Wayland Additive. We are also increasing our presence in Asia and are frequently represented at, or directly attending, tradeshows and conferences in the region in cooperation with our partners HTL in Japan and JPC in South Korea.”
“It is impressive to see how a small team from Uppsala is so well-known for its unique materials and production technology for wear-resistant applications. From having most of our sales activities in Europe, we now are seeing increasing business in North America, and we recently participated in the IMTS trade show in Chicago. Our activities in Japan and Korea are also creating new opportunities. The demand for hard, additively manufactured materials is high, both in the food and process industries, as well as in the automotive, defence and tooling sectors. This growing demand, in combination with our continuously improving offer, speaks for an exciting future!”, says Magnus Bergman, CEO of VBN Components.
Merry Christmas to you all!
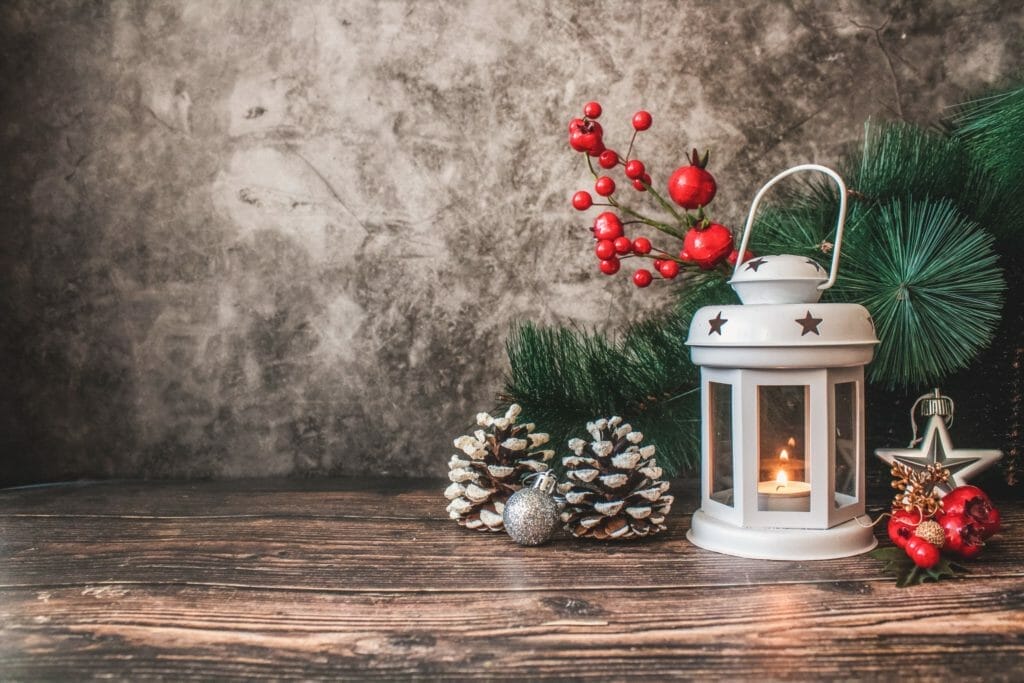