VBN Components is the first company in a very long time that can manufacture components in highly improved metals. The unique 3D-printing also enables production of complex shapes which would be too difficult to process in traditional production. In addition, VBN Components produces harder materials than anyone else in the business.
VBN Components attracted great attention during the well-established conference VDI Wissensforum in Bonn, earlier this year. The response was enormously positive when Chief Technical Officer Ulrik Beste gave a well-attended speech about the company’s wear-resistant materials, that, in addition, are 3D-printed.
The company was invited to present the unique group of Vibenite materials at VDI Conference of Transmissions in Commercial Vehicles. The fair is part of an established series of qualified, invited speakers where 1500 experts in transmission systems from all over the world are reunited yearly.
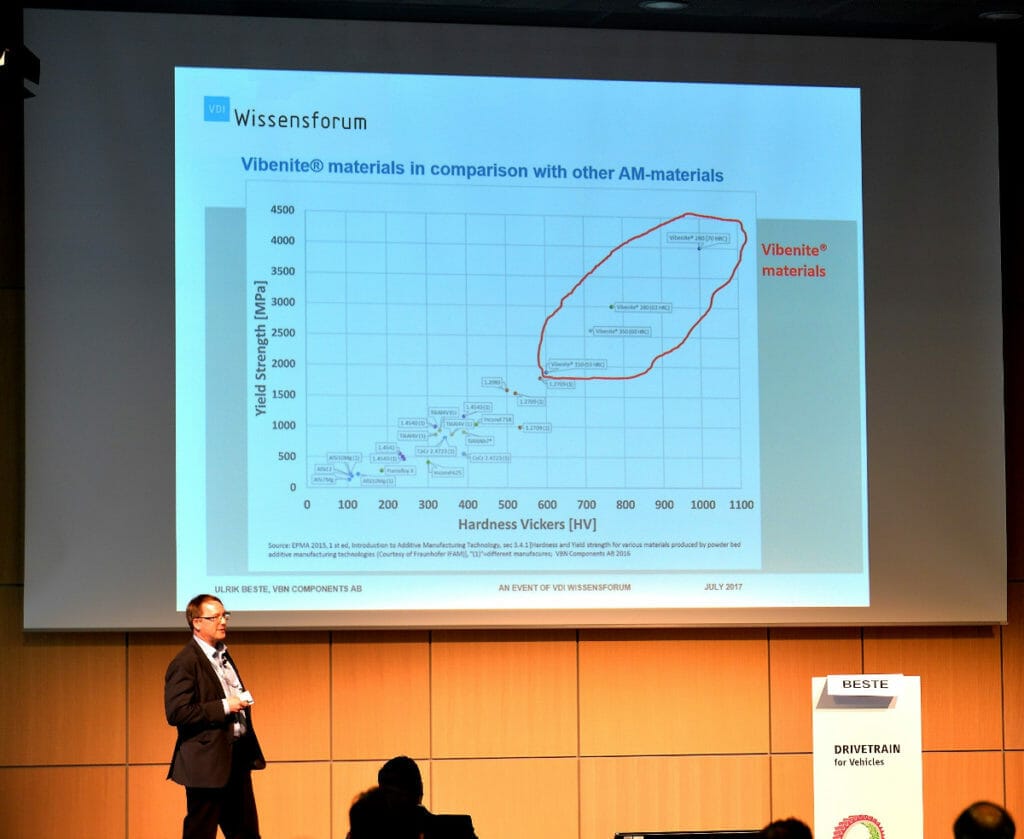
Ulrik Beste presents VBN Components at Wissensforum.
– It’s a particular feeling to introduce our news to a world where everyone speaks of 3D-printing, but where Chief Scientific Officers from large companies need to ask multiple times if it’s really true that we can make better materials than the traditional ones. And, on top of it, that they’re 3D-printed, says Ulrik Beste, Chief Technical Officer at VBN Components.
VBN Components in brief
VBN Components AB is a frontline, material developing company that manufactures wear-resistant metal components directly from powder, a.k.a. 3D-printing (additive manufacturing, free forming). The company has won a number of awards and is performing a range of important customised projects to improve the competitiveness of the engineering industry. VBN provides Near-Net-Shape components branded Vibenite® to clients in need of metal components with high complexity and/or extreme wear-resistance. www.vbncomponents.com