Dear friends,
After a calmer summer period we are now back full-time, facing an eventful end of the year. Our cemented carbide Vibenite® 480 has been nominated for an award, we are soon off to Germany for a big trade fair, and we are introducing the exciting product development Vibenite® Combo.

Finalist TCT Awards
In July it was announced that our cemented carbide “Vibenite® 480” is a finalist at the prestigious TCT Awards. The winner will be announced on September 25th at the National Conference Centre in Birmingham, UK.
“We are delighted to have beaten off the 100’s of entries and to have been listed as a finalist at the TCT Awards, that showcase world leading projects within additive manufacturing”, states CEO Martin Nilsson.
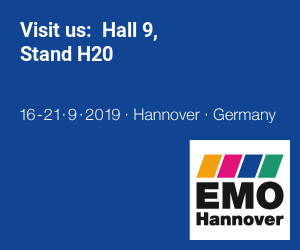
Exhibiting at EMO
EMO Hannover is one of the world’s leading metal working fairs. This year 130.000 visitors are expected during the six days of the fair. On 16-21 September, VBN Components will be exhibiting with the Additive Manufacturing Circle, Hall 9 – Stand H20. In December last year, VBN launched the cemented carbide Vibenite® 480, which will be the central piece for the fair. More than 1000 people have already watched the two videos about the material, so join them to learn more! Get in touch with us on info@vbncomponents.com to book a meeting at the fair.
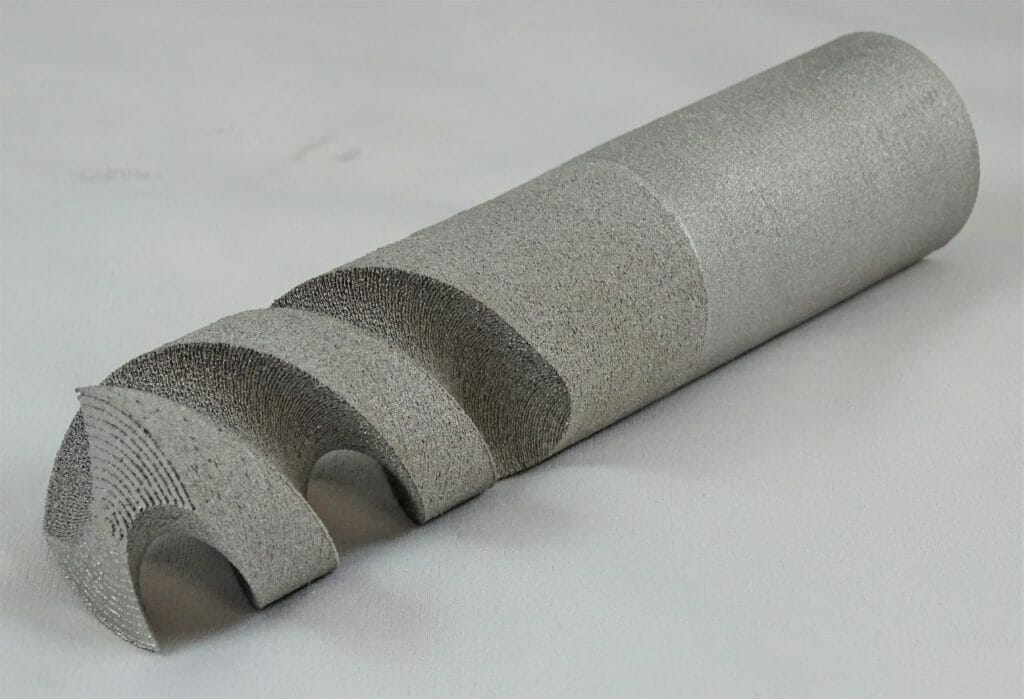
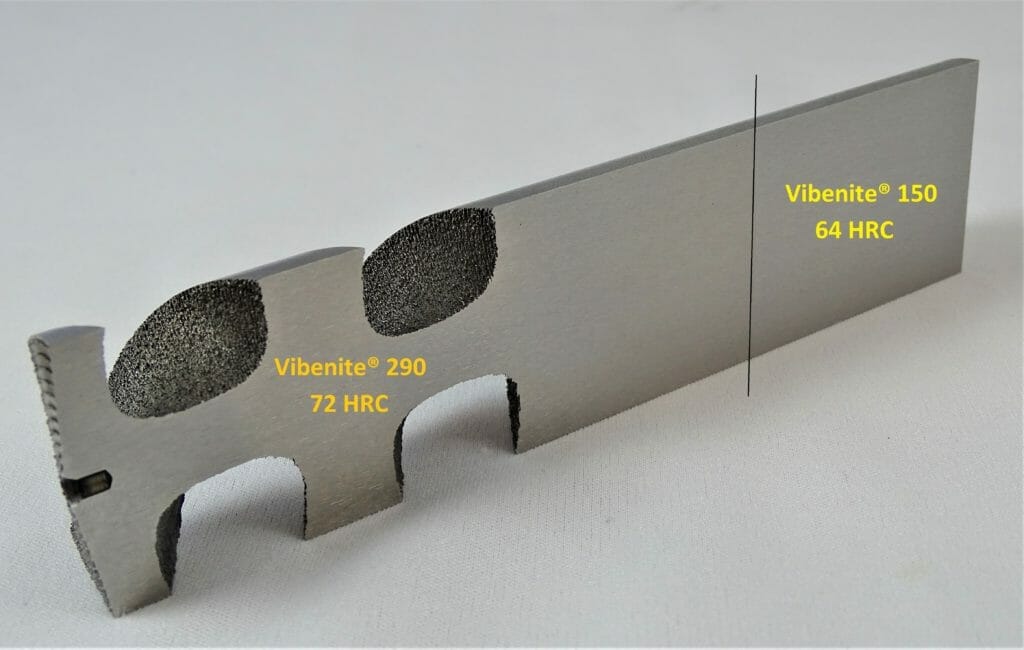
Vibenite® Combo
In some applications, our customers are looking for different properties
in the same component. We have, therefore, developed Vibenite® Combo,
that combines the toughness of Vibenite® 150 with the extreme hardness
of Vibenite® 290, the world’s hardest steel. This has been accomplished
by printing Vibenite® 290 upon an already printed cylinder of Vibenite®
150.
“By using our thorough additive printing knowledge in Electron Beam
Melting, we have been able to combine the materials. This makes it
possible to have extreme toughness in one part and extreme hardness and
wear resistance in another. Of course you still keep all the benefits of
additive manufacturing such as the option of integrating channels or
other complex structures”, says Ulrik Beste, CTO of VBN Components AB.
Achieving the desired quality of the material combination has been
demanding. VBN tested a long range of settings to finally be able to
attach the materials to one another. In order to get a fully crack- and
pore-free weld, it was necessary to gain control of the thermal
expansions of the two materials.