Press release 29 June 2020
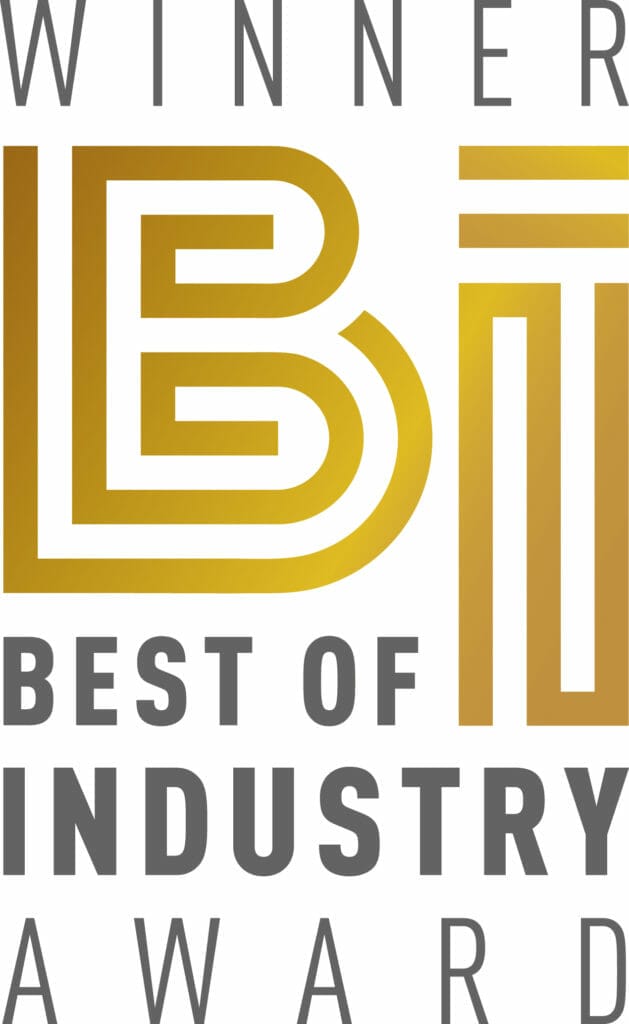
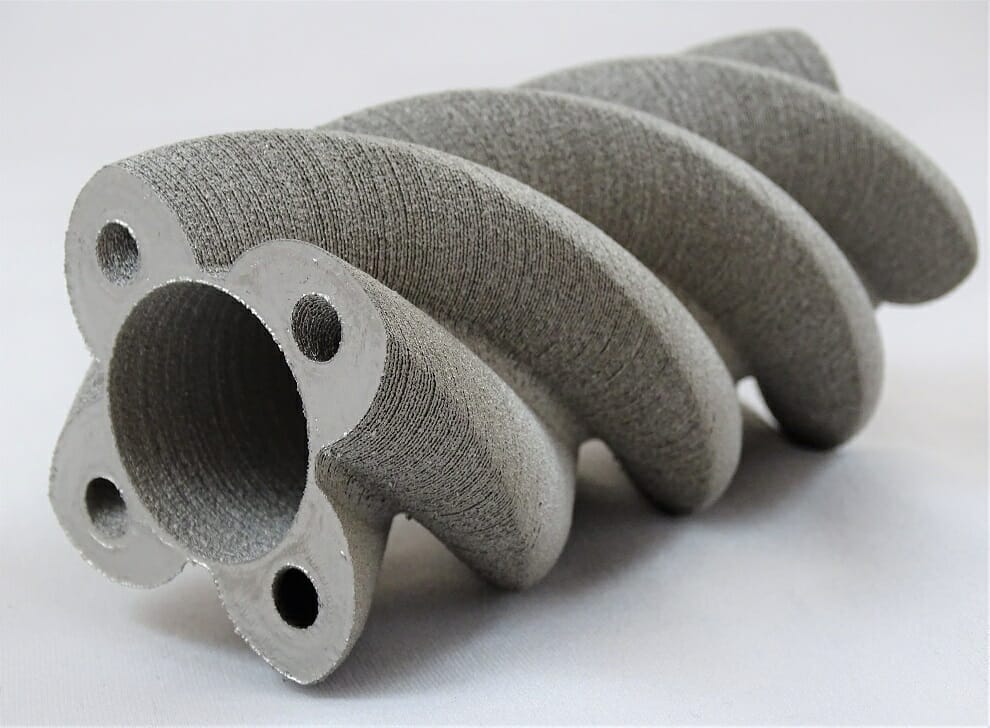
A hard metal (cemented carbide) produced with new shapes and functions, without sintering or cutting. Minimal material waste. A patented alloy that is heat resistant up to 750°C. After years of research, VBN Components is the first company to succeed with this innovation.
Swedish VBN Components develops new materials with extreme wear and heat resistance, produced with 3D printing. For more than a decade the company has been pioneering the metal industry. The latest innovation, the cemented carbide Vibenite® 480, has now been awarded with the German “Best of Industry Award” in the category of additive manufacturing. The alloy is corrosion resistant and also extremely heat and wear resistant. The fact that it is produced by additive manufacturing / 3D printing is absolutely ground-breaking. It enables complex shapes for industrial tools and components and reduces environmental impact to an absolute minimum.
- Germany is a very important market for us, and we are delighted to accept this award. We have always strived to develop materials that offer uniqueness and improved performance, and the Best of Industry Award is a great recognition to our achievement, says Ulrik Beste, PhD Materials Science and Tribology, CTO of VBN Components.
Increased productivity and reduced environmental impact
Vibenite® 480 is based on metal powder produced through large scale industrial gas atomisation. This minimises both cost and environmental impact. The new material combines the toughness of powder metallurgy high speed steels (PM-HSS) with the heat resistance of cemented carbides, which is why this new group of materials is named hybrid carbides. Within 3D printing it was always a wish to produce alloys with high carbide content. VBN Components has proved that they definitely master this technique, as the only company world-wide. Their Vibenite® 480 has a carbide content of ~65%, making it tougher than regular hard metals and therefore suitable for more complex details. Typical applications for Vibenite® 480 are therefore cutting tools for milling, drilling and gear cutting, which require good wear resistance at high temperatures combined with good toughness. The 3D printing process opens up completely new possibilities in the design of the tools.
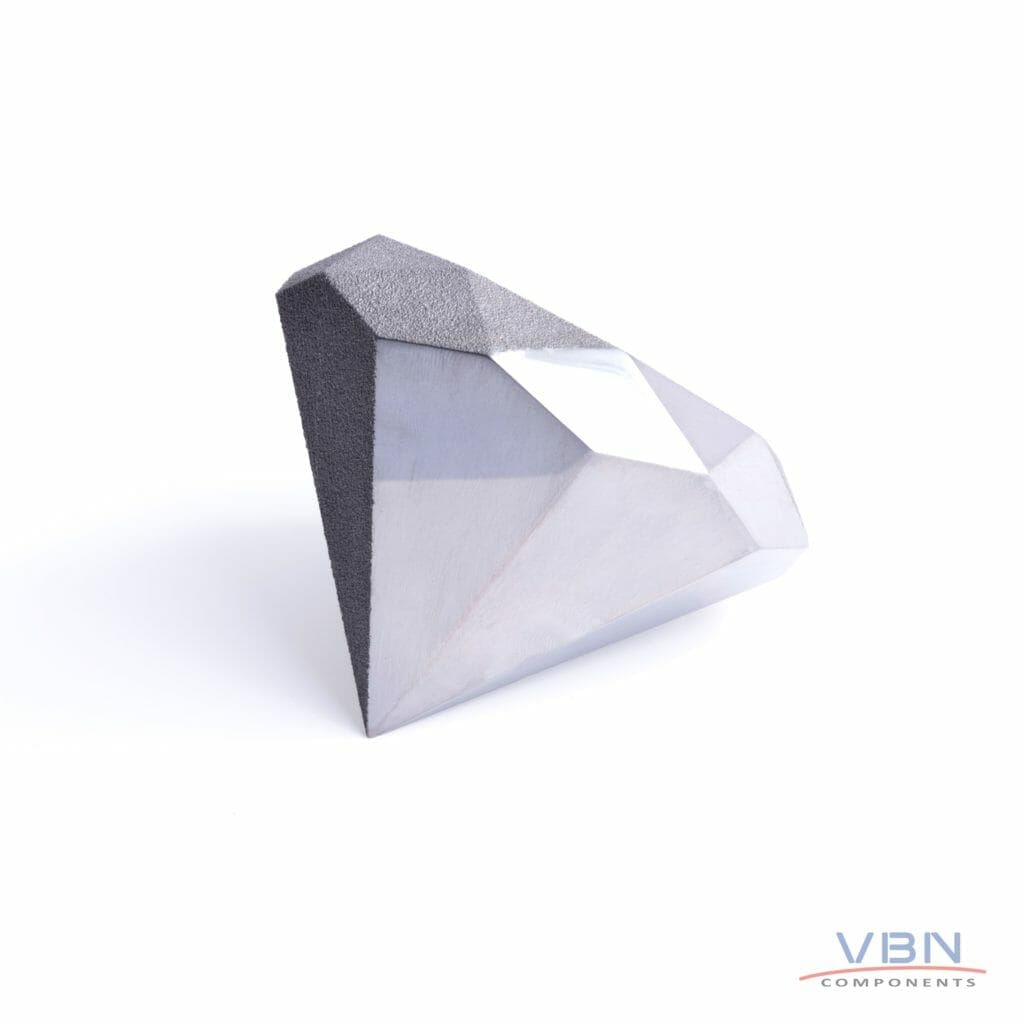
Vibenite® 480 is also suitable for all components that are subject to high wear, such as pump components, nozzles and baffle plates. – An ideal alternative to hard metals or wear-resistant alloys. Thanks to the 3D printing process, the components can rapidly be produced in near-net-shape. The design options of 3D printing offer new approaches to make components even more wear resistant. 3D printed cutting tools or wear components can be manufactured with very short lead times, which opens for many new approaches to build, test and improve prototypes and finally take the optimised component or cutting tool to serial production.