Dear VBN Friends,
Welcome to the latest edition of the VBN Components AB newsletter! We have had an eventful period, filled with significant contributions and participations in various events globally. Our team hosted two engaging webinars in September entitled “What can you 3D Print with the world’s hardest steel?” Additionally, we proudly exhibited at EMO Hannover, and Formnext Forum Tokyo through our partner HTL, and our CTO Ulrik Beste shared his insights as a plenary speaker at the 28th International Conference on Materials and Technology (28 ICM&T).
CEO Magnus Bergman took the stage at the Tech Stage at Formnext Frankfurt, where we introduced our groundbreaking high-performance materials development service. Magnus Bergman also represented us at Empa in Dübendorf/Zürich with Business Sweden and others at the Swiss-Swedish Innovation Initiative. His presence was also felt at the Elmia Subcontractor fair with the Innovative Materials Arena. Moreover, we are now engaged in an Industrial PhD Collaboration with Uppsala University, which you can read more about below.
Advancing materials development: A VBN endeavour
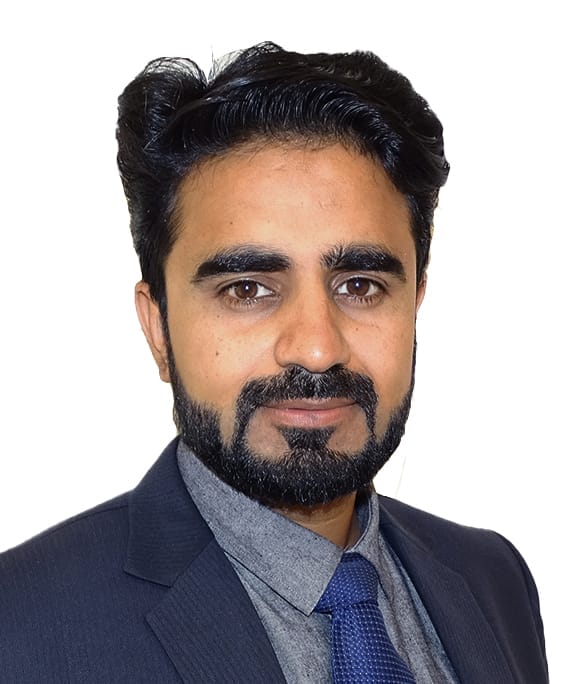
VBN Components is making remarkable progress in the field of advanced metal additive manufacturing, with an emphasis on innovative materials development and strategic industrial collaborations. Our latest venture includes an Industrial PhD collaboration with the Ångström Laboratory at Uppsala University, focusing on “Spatially controlled structural variations” in wear-resistant 3D-printed metals.
Saad Khalid, an MSc graduate from Uppsala University, leads this research, under the supervision of VBN’s CTO, Ulrik Beste.
The project, co-financed by WISE and the Knut and Alice Wallenberg Foundation, seeks to tailor materials for enhanced performance and sustainability. Our CEO, Magnus Bergman, underlines the rarity for an SME to offer such a research position, demonstrating our dedication to unique materials development. Read press release.ttending the special EMO conference on the Indian tool market, as we see this as an exciting opportunity. Come to Hall 9 Stand F02 to discuss our wear-resistant alloys!
Materials development as a service
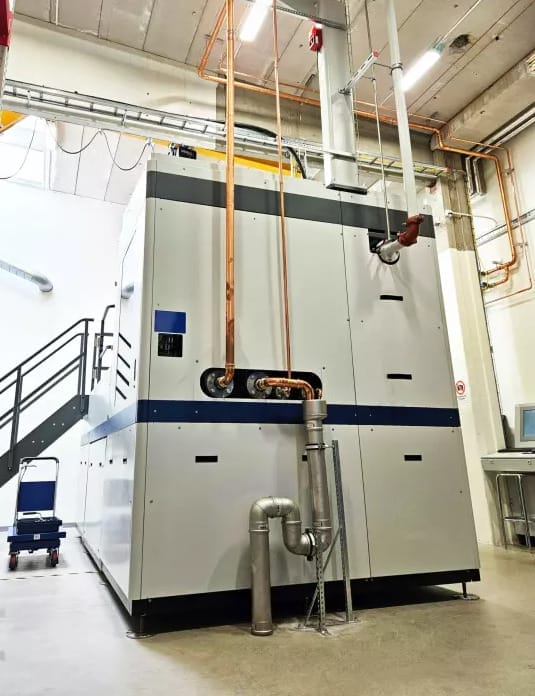
Our commitment to materials development was showcased at Formnext 2023, where we introduced “High-Performance Materials Development” as a Service. This service explores the capabilities of hard metals and refractories in additive manufacturing, utilising our expertise in high-carbon steels and materials like Tungsten and Niobium. CTO Ulrik Beste highlights the service’s significance in advancing the limits of metal additive manufacturing. This initiative aligns with VBN’s broader strategy to address the evolving requirements of the industry, offering tailored materials development to our clients.
Central to this is our URQ-HIP (Uniform Rapid Quenching-Hot Isostatic Pressing) machine, which enables unique heat -treatment possibilities, ensuring pore-free materials and furthering alloy development. This not only accelerates delivery times but also aligns with VBN’s sustainability goals through the minimisation of heating and transport, and a recycling system for process gas.
Extreme hardness of Vibenite® 290
VBN has previously demonstrated that Vibenite® 290 is the world’s hardest steel with a hardness of 72 HRC. In experiments conducted earlier this year with the newly installed combined HIP and Hardening unit, it was established that it was feasible to further increase the hardness using the patented heat treatment method. Now, in December, VBN has supplied the first metal cutting components made from Vibenite® 290, achieving a hardness of 1200 Vickers, which corresponds to approximately 74.5 HRC (this is an approximate conversion, as it is not possible to measure Rockwell hardness at such elevated levels).
Industrialisation of surface treatment
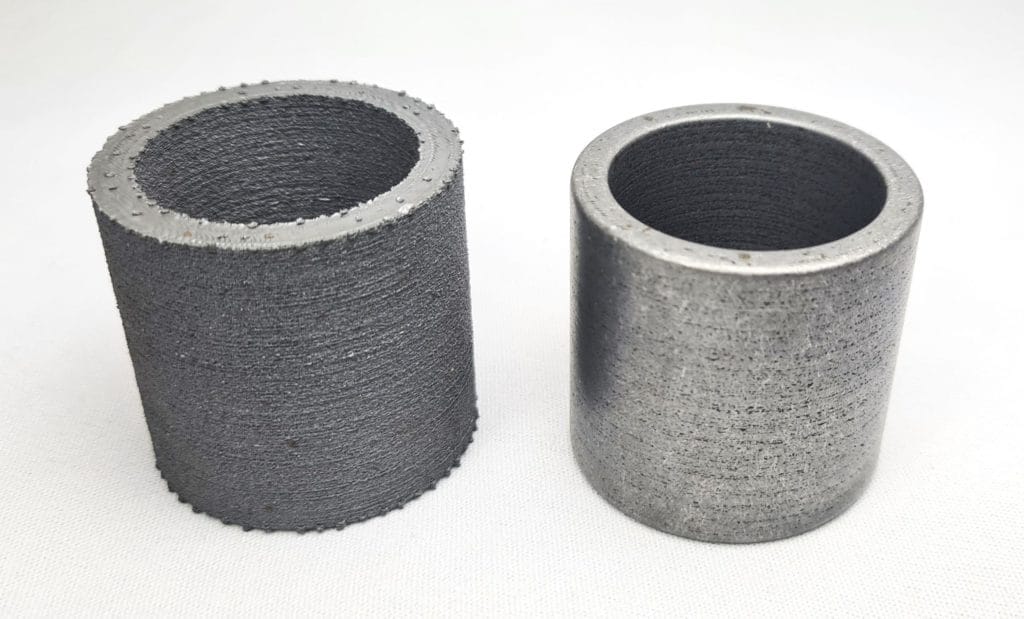
Over recent years, VBN has tested various post-surface treatment techniques. The objective is, of course, to reduce surface roughness, thereby minimising the need for grinding or other forms of post-processing, and to enhance the fatigue resistance of surfaces that are not ground. Here is an example of the highly positive impact of chemical tumbling at one of VBN’s suppliers. On the left, we see a printed tube with a surface roughness value of approximately 30 µm, and on the right, the same tube after post-processing, achieving an Ra value of about 3 µm. VBN has utilised this process in tubes, rings, and various metal cutting tools across a range of different Vibenite® alloys. If you would like more information, please do contact us.
Plenary speaker at Conference on Materials and Technology
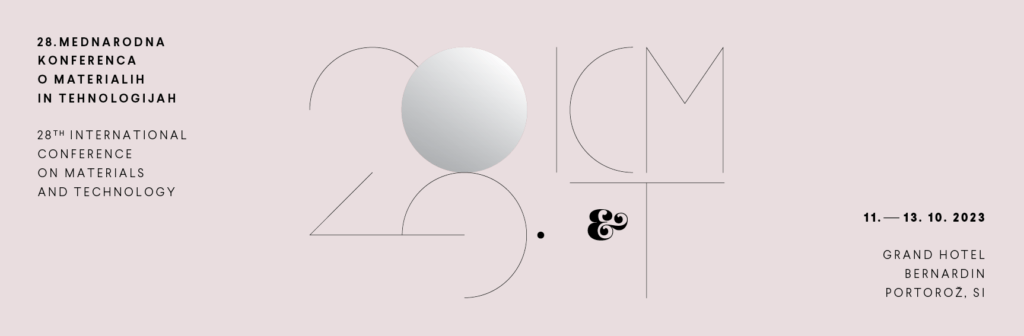
28th International Conference on Materials and Technology (28 ICM&T) was a meeting of professionals from research institutes, universities and industry that are active in the fields of: metallic materials, biomaterials, 3D-printed materials, etc. Ulrik Beste, CTO of VBN Components, was one of the plenary speakers at the conference and gave the lecture “Additive Manufacturing as the revolution of wear resistant metals.”
Workshop on mining and processing reliability issues
Mining and processing equipment reliability issues, caused by wear, are an industry-wide issue. On 5 December VBN took part in a virtual workshop where our CTO Ulrik Beste highlighted the benefits of Vibenite® materials in this aspect. VBN was one of seven companies and agencies approaching the issue. The workshop was organised by the Canadian Mining Innovation Commercialization Accelerator (MICA) and their partners at InnoTech Alberta to showcase new commercial technologies that have been designed to meet the demands of the mining industry, and that keep equipment running and reliable.
Swiss-Swedish Innovation Initiative
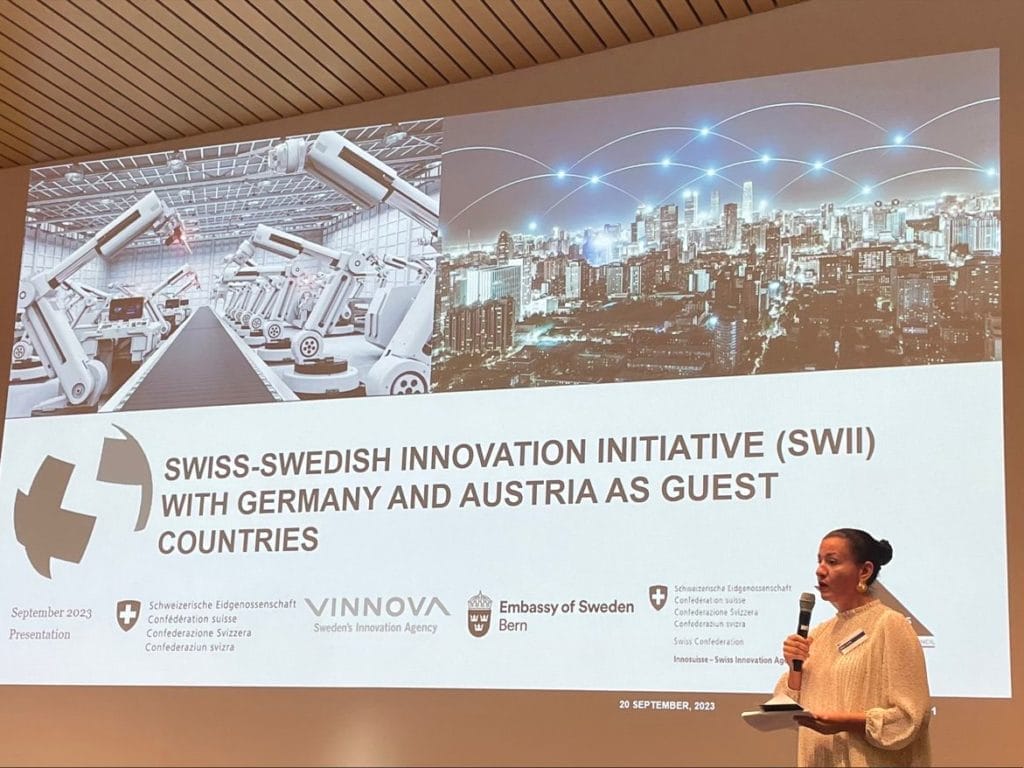
VBN, represented by CEO Magnus Bergman, has been selected to participate in the Swiss-Swedish Innovation Initiative, which has the overall objective to increase market oriented high-technology R&D projects between Switzerland and Sweden. In September, a networking day at Empa Materials Science and Technology Research Institute in Dübendorf/Zürich, Switzerland, was organised with Business Sweden to strengthen relations further.
Merry Christmas and a Happy New Year to you all!
This year we have donated gift cards as Christmas presents to families that would otherwise be left without, through the charity Uppsala Stadsmission.
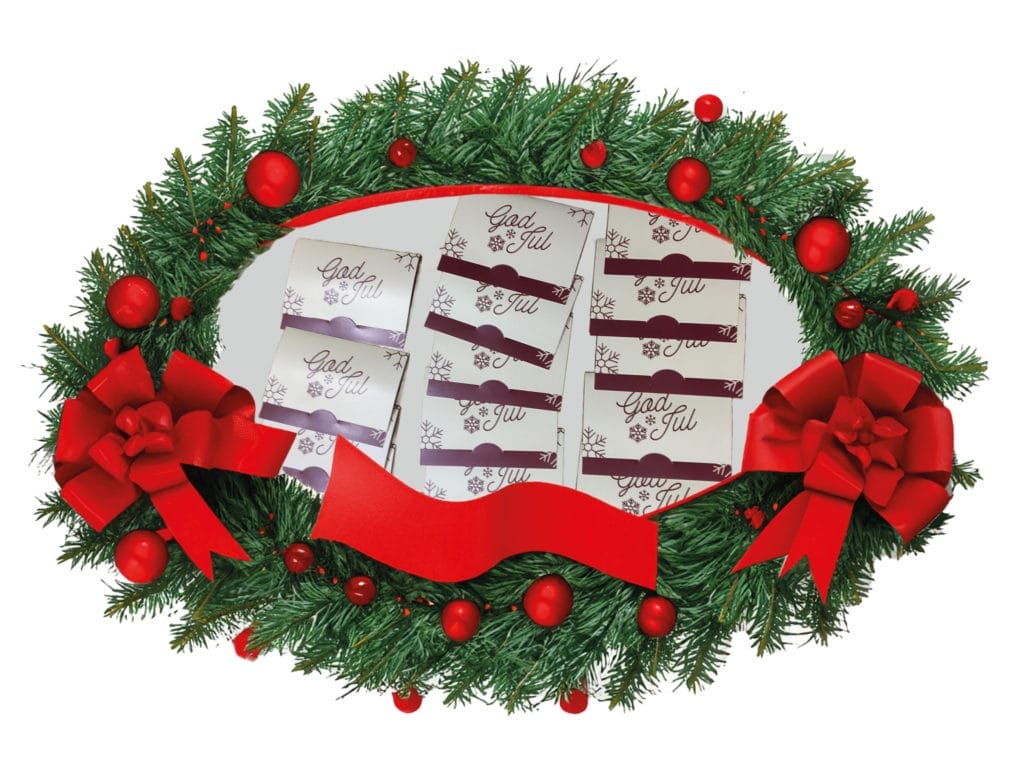